Going with the Flow—Industrial Water Conservation Tips
By Brian on July 4, 2025
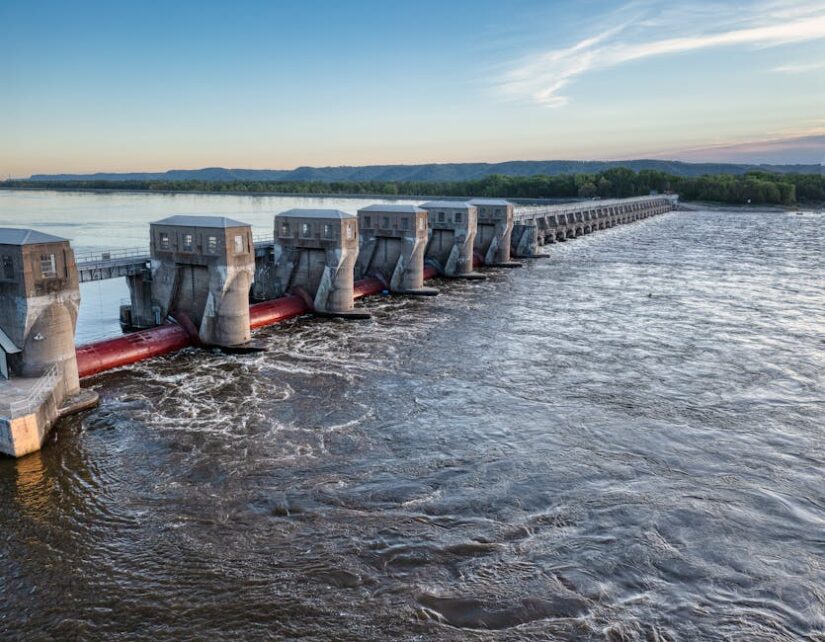
Why Industrial Water Conservation is Critical for Your Business
Industrial water conservation is the practice of reducing water consumption in manufacturing, processing, and commercial facilities through efficient equipment, smart monitoring, and water reuse strategies. With industrial facilities accounting for 5-10% of global freshwater withdrawals, conservation efforts can cut water usage by up to 30% while delivering significant cost savings.
Key Industrial Water Conservation Strategies:
- Equipment upgrades – High-efficiency fixtures, closed-loop cooling systems, and automated shut-off nozzles
- Water reuse – Recycling boiler condensate, cooling tower blowdown, and process rinse water
- Smart monitoring – Real-time leak detection, flow meters, and AI-powered analytics
- Process optimization – Eliminating single-pass cooling and maximizing cycles of concentration
- Alternative sources – Rainwater harvesting and greywater systems for non-potable uses
The business case is compelling. Facilities typically see returns on investment within 2-3 years, with some measures paying for themselves in under 12 months. Beyond cost savings, water conservation helps companies meet environmental regulations, reduce drought risk, and build stronger community relationships.
For Northern California businesses facing increasing water scarcity and rising utility costs, industrial water conservation isn’t just good practice – it’s essential for long-term resilience.
Industrial water conservation terms simplified:
What you’ll learn
In this comprehensive guide, we’ll walk you through proven strategies for implementing industrial water conservation in your facility. You’ll find step-by-step approaches to reduce water consumption, from simple retrofits to advanced reuse systems. We’ll cover the environmental and economic benefits, show you how to audit your current usage, and provide practical solutions that deliver measurable results.
Industrial Water Conservation: Why It Matters
Water is becoming the new oil—and smart businesses are paying attention. Here in Northern California, we’ve seen how drought conditions can impact operations and costs. Industrial facilities consume 5-10% of global freshwater withdrawals. By 2030, as the world population reaches 9.8 billion, industrial water use could jump to 15-20% of global withdrawals.
The regulatory landscape is shifting too. Many areas now require recycled water for new industrial construction. Companies that get ahead of water conservation build trust with neighbors and regulators, while those that lag behind face increasing scrutiny and potential restrictions.
The economic case for conservation is incredibly strong. When you save water, you’re also cutting costs for electricity, gas, chemicals, and wastewater disposal. A well-planned approach to industrial water conservation can slash usage by up to 30%, with many facilities seeing their investments pay off in under two years.
Environmental & social stakes of industrial water conservation
Your facility’s water use ripples far beyond your property line. When we pump too much groundwater, we’re draining aquifers that took thousands of years to fill. Heavy surface water withdrawals stress rivers and the wildlife that depends on them. In Northern California, our salmon runs need adequate stream flows to survive—making industrial water conservation a direct contribution to biodiversity.
Community relationships matter more than ever. Local residents dealing with water restrictions while nearby industrial facilities continue high consumption creates tension that no business wants to face. Smart companies recognize that water conservation isn’t just good for the environment—it’s good for their reputation and community standing.
Economic case for industrial water conservation
The financial benefits of industrial water conservation are both immediate and long-lasting. Scientific research on cost benefits shows that water reuse investments often pay for themselves within the first year.
Consider these real-world examples: replacing high-volume hoses with high-pressure, low-volume cleaning systems can save up to 25% of total water consumption. Converting from single-pass cooling to closed-loop systems can reduce water use by 90%. Installing efficient fixtures and aerators typically pays for itself within 12-18 months.
The savings go beyond your monthly utility bill. Conservation reduces insurance risks related to water scarcity and improves your operational resilience during drought periods. Many utilities sweeten the deal with rebates and incentives for water-efficient equipment, making your return on investment even better.
Mapping Your Water Footprint—Audits, Data & Smart Monitoring
You can’t manage what you don’t measure. Before diving into any industrial water conservation project, you need to understand exactly where every drop goes in your facility. A comprehensive water audit is your starting point—creating a complete picture of how water flows through your operation.
The old-school approach involves walking around with a clipboard, jotting down meter readings, and hoping you catch problems before they become expensive disasters. Modern smart monitoring systems change the game completely.
Manual Audits | Real-Time Digital Monitoring |
---|---|
Quarterly or annual assessments | Continuous 24/7 monitoring |
Manual meter readings | Automated data collection |
Delayed leak detection | Immediate alerts for anomalies |
Limited data granularity | Detailed usage patterns |
Lower upfront costs | Higher ROI through early problem detection |
Smart monitoring systems use IoT sensors, flow meters, and pressure monitors to keep tabs on your water usage around the clock. These systems can spot a leak within minutes rather than weeks, catching small problems before they become big headaches.
Setting up a best-practice industrial water conservation audit
Starting your audit means creating detailed flow diagrams that map every water source and destination in your facility. Begin by identifying all your water inputs—where it comes from and how much you’re using. Then follow the water through your processes, noting volumes, treatment requirements, and where it eventually goes.
The key performance indicators (KPIs) that matter most include your total water consumption per unit of production, water loss percentages, and cooling tower makeup water rates. You’ll also want to track process water recycling percentages and identify your peak demand periods.
More info about Water Conservation Services can help you design an audit program that fits your specific facility needs. Professional auditors bring specialized equipment like ultrasonic flow meters and thermal imaging cameras that can spot leaks hiding in walls or underground pipes.
Leveraging smart tech & AI for continuous improvement
Artificial intelligence isn’t just for self-driving cars—it’s revolutionizing water management too. AI-powered dashboards analyze your usage patterns, predict when equipment might fail, and automatically optimize system performance.
These systems excel at spotting subtle changes in flow rates that signal developing problems. Predictive analytics take it a step further, forecasting water demand based on your production schedules, weather patterns, and historical usage data.
Latest research on smart water platforms shows that AI-powered systems can reduce water consumption by an additional 10-15% beyond traditional conservation measures. The smartest systems even integrate with weather forecasts to optimize irrigation schedules and cooling tower operations.
Proven Strategies & Technologies to Reduce Water Use
When it comes to industrial water conservation, the smartest approach combines immediate wins with strategic long-term investments. The beauty of modern water conservation technology is that it’s designed to work with your existing processes, not against them.
High-efficiency fixtures drop right into place where your old ones were. Closed-loop cooling systems can often retrofit into existing equipment. Advanced technologies like high-efficiency reverse osmosis (HERO) systems are game-changers for facilities that need large volumes of treated water.
The secret sauce is prioritizing based on your specific situation. Quick-win retrofits provide immediate relief for your water bills and generate the savings to fund those bigger upgrades that really move the needle.
Quick-win retrofits for industrial water conservation
Let’s start with the low-hanging fruit—the changes that cost little but save a lot. These are the projects that make your CFO smile because they pay for themselves so quickly.
Fixture upgrades are probably the easiest place to start. Installing faucet aerators and low-flow showerheads in employee areas takes about five minutes per fixture but can cut water use by 30-50%. Dual-flush toilets give people the choice between a light flush and a full flush. Motion-activated faucets eliminate the biggest source of waste in break rooms and restrooms: fixtures left running.
Equipment modifications deliver bigger savings with minimal effort. Automatic shut-off nozzles on all hoses prevent 8-12 gallons per minute from going down the drain when someone walks away. Trigger-operated spray guns with adjustable pressure settings let your team use exactly the right amount of water for each task.
The smartest operational changes often don’t require any new equipment at all. Switching from water-based to dry cleaning methods where possible saves enormous amounts. Pre-cleaning cycles that remove heavy soils first mean less water needed for the final rinse.
These retrofits typically cost less than $10,000 for most facilities but can slash water consumption by 15-25%. Most pay for themselves within 18 months.
Process upgrades with bigger payoffs
Once you’ve captured the easy wins, it’s time to think bigger. These investments require more upfront capital, but they transform your entire water footprint.
Cooling system improvements offer the biggest bang for your buck in most industrial facilities. Converting single-pass cooling to closed-loop recirculating systems can cut cooling water use by 90% or more. High-recovery reverse osmosis systems for makeup water treatment reduce waste while improving water quality. Maximizing cycles of concentration in cooling towers can reduce water use by 25% with just better monitoring and control.
Advanced treatment systems let you reuse water that would otherwise go down the drain. Membrane bioreactors treat wastewater right on-site so you can reuse it in your processes. Ion exchange systems produce ultra-pure water with minimal waste.
Scientific research on operational planning shows that systematic process optimization can reduce industrial water conservation needs by 40-60% in many applications.
The upfront investment for major process upgrades ranges from $50,000 to $500,000 depending on your facility’s size and complexity. These projects typically pay for themselves within 3-5 years, while also improving process reliability and product quality.
Closing the Loop—Reuse, Recycling & Alternative Sources
One of the smartest moves you can make in industrial water conservation is to stop thinking of water as a single-use resource. Every drop that flows through your facility has the potential for a second life—and sometimes a third or fourth.
The beauty of water reuse lies in its simplicity. That crystal-clear boiler condensate you’re sending down the drain? It’s essentially distilled water that took energy to create. The cooling tower blowdown you’re discharging? It’s perfect for watering your landscaping.
Smart facilities are already capturing these streams and putting them back to work. A typical manufacturing plant can reduce its freshwater consumption by 30-50% just by reusing what it already produces. The economics are compelling too—most reuse systems pay for themselves within two to three years.
Alternative sources like rainwater harvesting and greywater systems open up even more possibilities. A properly designed rainwater collection system can handle 50-70% of your non-potable water needs, especially here in Northern California where we get most of our rain during a few concentrated months.
In-plant reuse streams that make sense
The best reuse opportunities are often hiding in plain sight. Start by walking through your facility and asking: “Where does this water go after we use it?”
Boiler condensate is pure gold in the water world. It’s already been treated, heated, and cooled—essentially distilled water that’s perfect for reuse in steam systems. Many facilities lose thousands of gallons of this high-quality water every day simply because they haven’t installed a condensate return system.
Final rinses from cleaning operations might not be clean enough for drinking, but they’re often perfect for initial rinses in the next cleaning cycle. Food processing plants have been doing this for decades—the last rinse becomes the first rinse, cutting water use in half.
Cooling tower blowdown contains dissolved minerals that make it unsuitable for continued cooling use, but those same minerals can actually benefit your landscaping. With basic pH adjustment, this water becomes excellent for irrigation.
More info about Water Conservation Solutions can help you identify which reuse streams make the most sense for your specific operation. Every facility is different, and the best opportunities depend on your processes, water quality, and local regulations.
Safe integration of non-potable sources
Here’s where things get serious—and where you absolutely need professional help. Cross-connection control isn’t just a good idea; it’s the law in most jurisdictions. You cannot risk contaminating your potable water supply, period.
The basic rule is simple: separate systems, separate pipes, separate everything. Non-potable water gets its own purple pipes, its own valves, and its own clearly marked connections.
Backflow prevention devices are your insurance policy against disaster. These mechanical devices ensure that water flows only in the intended direction, preventing contaminated water from entering your clean water supply.
Water quality testing becomes part of your routine when you’re reusing water. Different applications have different requirements, and you need to know your water meets those standards.
Staff training is absolutely critical. Everyone who works with these systems needs to understand the difference between potable and non-potable water, how to identify which is which, and what to do if something goes wrong.
Working with local health departments and water utilities early in the planning process saves headaches later. Most are supportive of water reuse projects—they just want to make sure they’re done safely.
Culture, Training & Overcoming Barriers
The truth is, industrial water conservation isn’t just about installing fancy equipment and hoping for the best. You could have the most advanced water monitoring system in the world, but if your employees don’t understand why it matters or how to use it properly, you’re basically throwing money down the drain—literally.
Your maintenance crew walks past a small leak every day for three months. That “tiny” drip wastes thousands of gallons and costs hundreds of dollars. But if they know why reporting leaks matters and feel empowered to act, that same leak gets fixed on day one.
The most successful facilities treat every employee as a water conservation partner. They provide clear training on daily practices that make a real difference, like properly shutting off hoses after use, following equipment shutdown procedures, and understanding how their specific job impacts water usage.
Recognition programs that reward conservation ideas often uncover the best savings opportunities. Your floor workers know where water gets wasted because they see it every day. When you create incentives for them to share those observations, amazing things happen.
Building a water-smart workplace
Creating a water-conscious workplace starts with leadership commitment that goes beyond just saying the right things. When managers actively participate in conservation efforts and regularly communicate about goals and achievements, employees pay attention.
Toolbox talks and safety meetings provide perfect opportunities to discuss water conservation alongside other operational topics. Instead of making it feel like another compliance requirement, frame it as part of being a responsible, forward-thinking workplace.
Visual reminders work incredibly well in industrial settings. Strategic signage near water-using equipment, conservation tips posted in break rooms, and dashboard displays showing real-time usage help keep conservation visible and top-of-mind.
Regular maintenance routines form the backbone of any successful conservation program. Training your maintenance staff on proper system operation isn’t just about fixing problems—it’s about preventing them.
Financing barriers are a common concern. Many facilities want to implement conservation measures but struggle with upfront costs. The good news is that creative financing solutions exist. Many utilities offer substantial rebates for water-efficient equipment, and some facilities use energy service companies to fund upgrades through guaranteed savings.
Phased implementation approaches can also spread costs over time while demonstrating early wins that build support for larger investments.
Frequently Asked Questions about Industrial Water Conservation
How much water can an average facility save?
Here’s the exciting news: most industrial facilities can slash their water consumption by 15-30% through smart conservation efforts. But here’s what makes it even better—many facilities actually exceed these targets once they get started.
The exact savings depend on where you’re starting from and how far you want to go. If your facility hasn’t focused on water efficiency before, you’re likely sitting on some fantastic opportunities. Quick-win retrofits like fixing leaks and installing efficient fixtures typically deliver 10-15% savings right off the bat.
But if you’re ready to think bigger, comprehensive programs that include process optimization and reuse systems can achieve 40-60% reductions. We’ve seen facilities in Northern California hit these numbers consistently when they take a systematic approach.
The secret sauce? Start with a thorough audit to find your biggest water-wasting culprits, then tackle improvements one step at a time. Many facility managers tell us they wish they’d started sooner once they see the results.
Will conservation hurt product quality?
This is probably the most common concern we hear, and honestly, it’s completely understandable. Nobody wants to risk their product quality to save a few dollars on water bills. But here’s what might surprise you: properly implemented water conservation measures actually improve product quality in many cases.
Think about it this way—closed-loop cooling systems provide more consistent temperatures than single-pass systems. High-efficiency treatment systems deliver cleaner, more consistent process water. When you match the right water quality to each specific application, you often end up with better results than the old “use potable water for everything” approach.
Now, some conservation measures do require careful monitoring. If you’re reusing rinse water, for example, you’ll want to keep an eye on quality standards. But with proper system design and monitoring, you can absolutely achieve both conservation and quality objectives.
The key is working with experienced professionals who understand both industrial water conservation and your specific industry requirements. That’s where proper planning and system design make all the difference.
What incentives or rebates are available?
You’re in luck—there are more incentives available than most facility managers realize. Northern California utilities are particularly generous with rebates because they understand that helping businesses conserve water benefits everyone.
Common incentives include rebates for high-efficiency fixtures and appliances, grants for water reuse system installation, and reduced connection fees for facilities using recycled water. Many utilities also provide free technical assistance for water audits and system design.
Local water districts often have their own programs on top of utility rebates. State agencies and federal programs add even more funding opportunities for industrial water conservation projects. The Database of State Incentives for Renewables and Efficiency (DSIRE) keeps current information on available programs, though it can be overwhelming to steer alone.
Here’s a pro tip: many rebate programs have limited funding that gets allocated on a first-come, first-served basis. The best time to apply is early in the budget year when funds are most available.
At Go Pro Plumbing, we help Northern California businesses steer these incentive programs and maximize their rebates. We’ve found that combining multiple incentives can sometimes cover 30-50% of project costs, making conservation upgrades even more attractive.
Conclusion
When you step back and look at the big picture, industrial water conservation really is a win-win situation. You’re cutting costs, helping the environment, and positioning your business for long-term success—all at the same time. With industrial facilities using up to 10% of the world’s freshwater, even small improvements at your facility can make a real difference.
The journey we’ve outlined doesn’t have to be overwhelming. Start with that comprehensive audit to see where you stand today. Then tackle the quick-win retrofits that’ll give you immediate savings and build excitement for bigger projects. As you see those first results rolling in, you can gradually expand to more sophisticated systems like water reuse programs and smart monitoring technology.
Here in Northern California, we’re all feeling the pressure from water scarcity and rising utility costs. The smart business owners we work with aren’t waiting for the next drought to hit—they’re getting ahead of the curve now. Companies that accept water efficiency today will enjoy competitive advantages through lower operating costs, smoother regulatory compliance, and stronger relationships with their communities.
That’s where we come in. At Go Pro Plumbing, we’ve been helping Northern California businesses steer these challenges for years. We’ve seen how the right conservation strategies can transform a facility’s water usage and bottom line. Our team knows the ins and outs of everything from basic fixture upgrades to advanced reuse systems.
What sets us apart is our commitment to making this process as smooth as possible for you. We handle everything from that initial audit through system installation and ongoing maintenance. Our comprehensive Services: Water Conservation are designed to help you achieve real, measurable results while keeping your operations running smoothly.
Whether you’re just starting to think about water conservation or you’re ready to dive into advanced systems, we’re here to help you every step of the way. We believe in same-day service and outstanding customer care—because your time is valuable, and water conservation projects shouldn’t slow down your business.
Ready to start saving water and money? Contact us today to learn how we can help your facility reduce consumption, cut costs, and build the kind of resilience that’ll serve you well in our increasingly water-conscious world. Let’s work together to make your business more efficient, more sustainable, and more profitable.